We don't move for you. We move with
you.
Atlas® International moving companies aren’t just movers and packers. We’re the helping hand that puts your new world within reach.
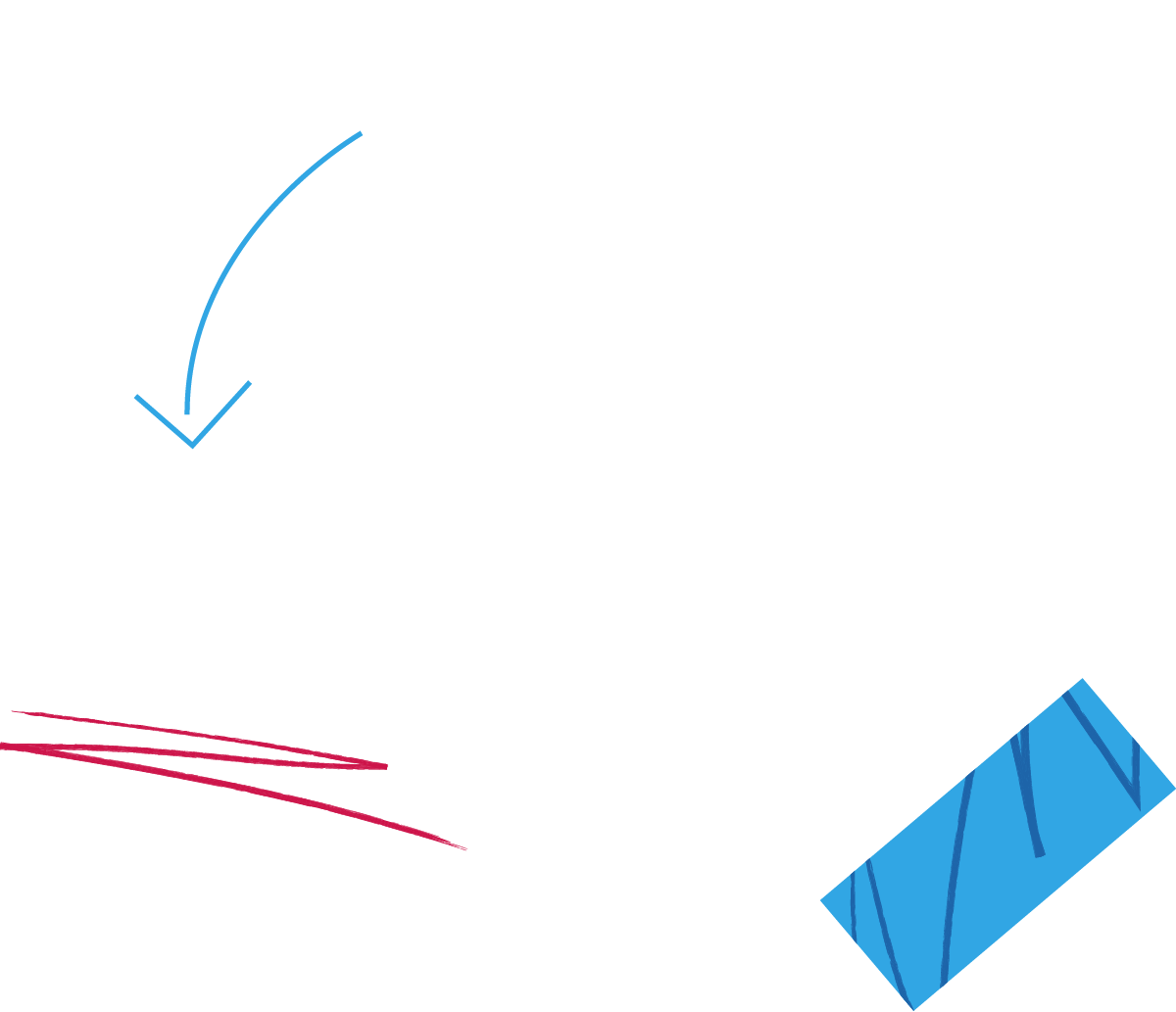
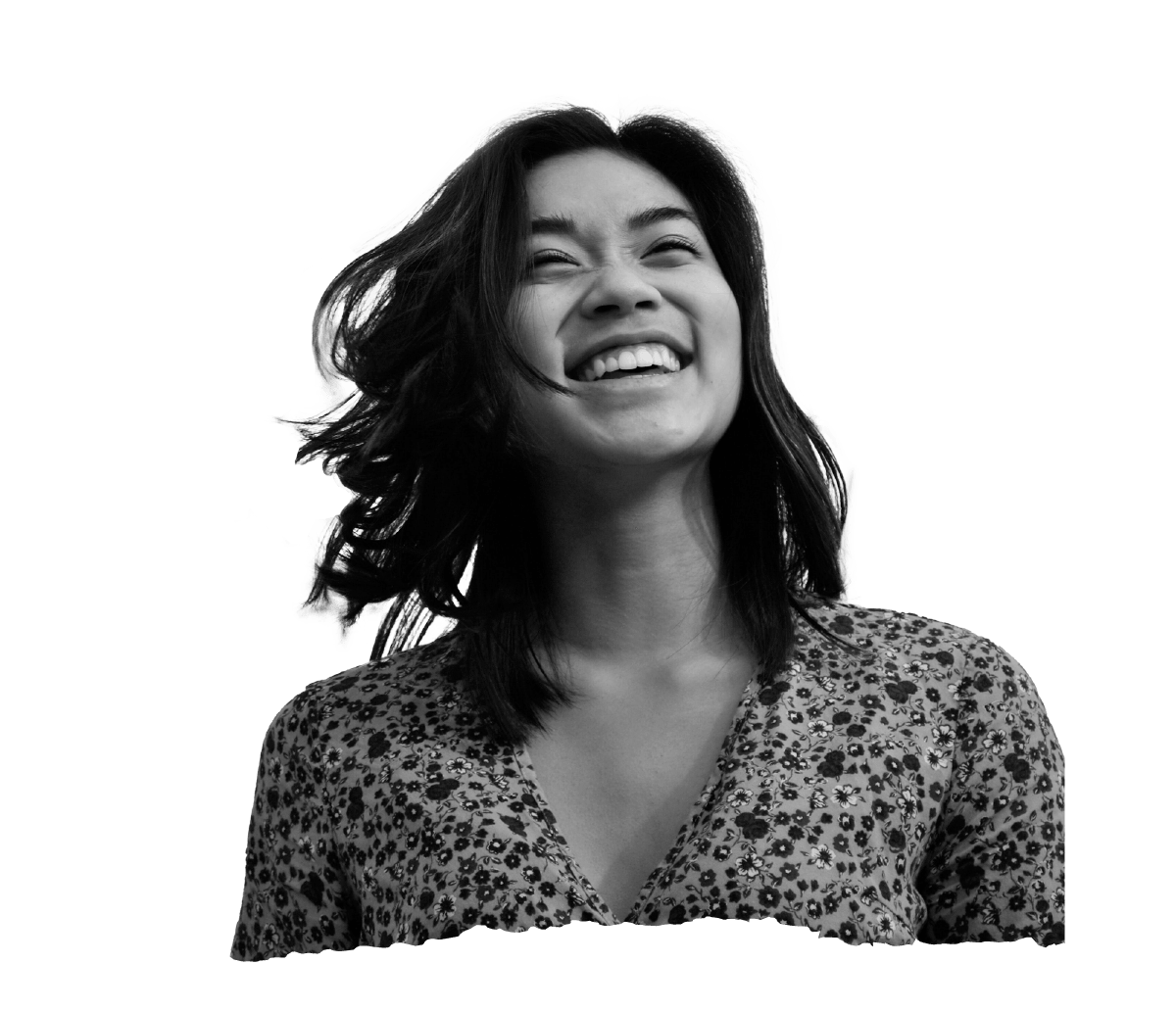
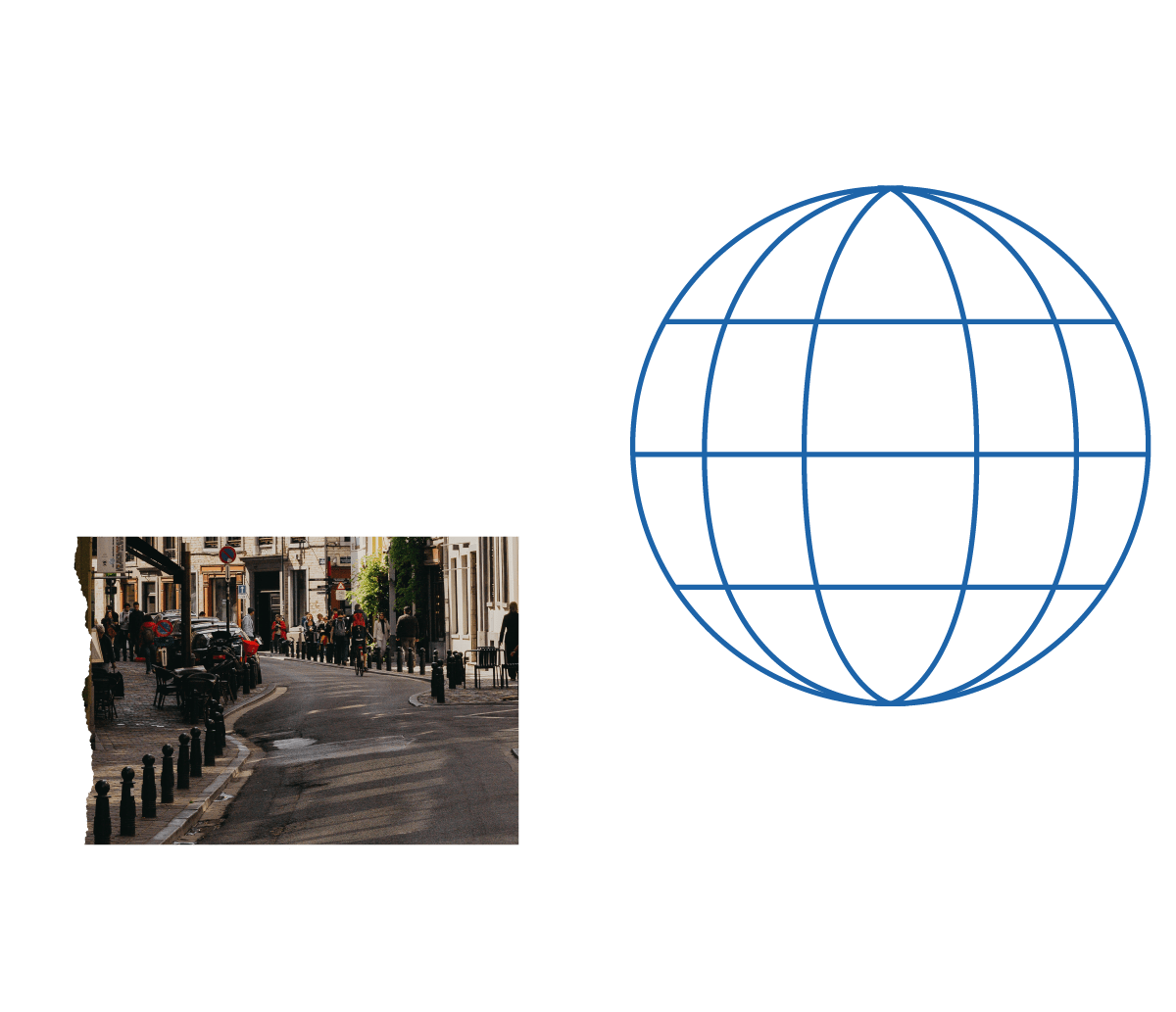
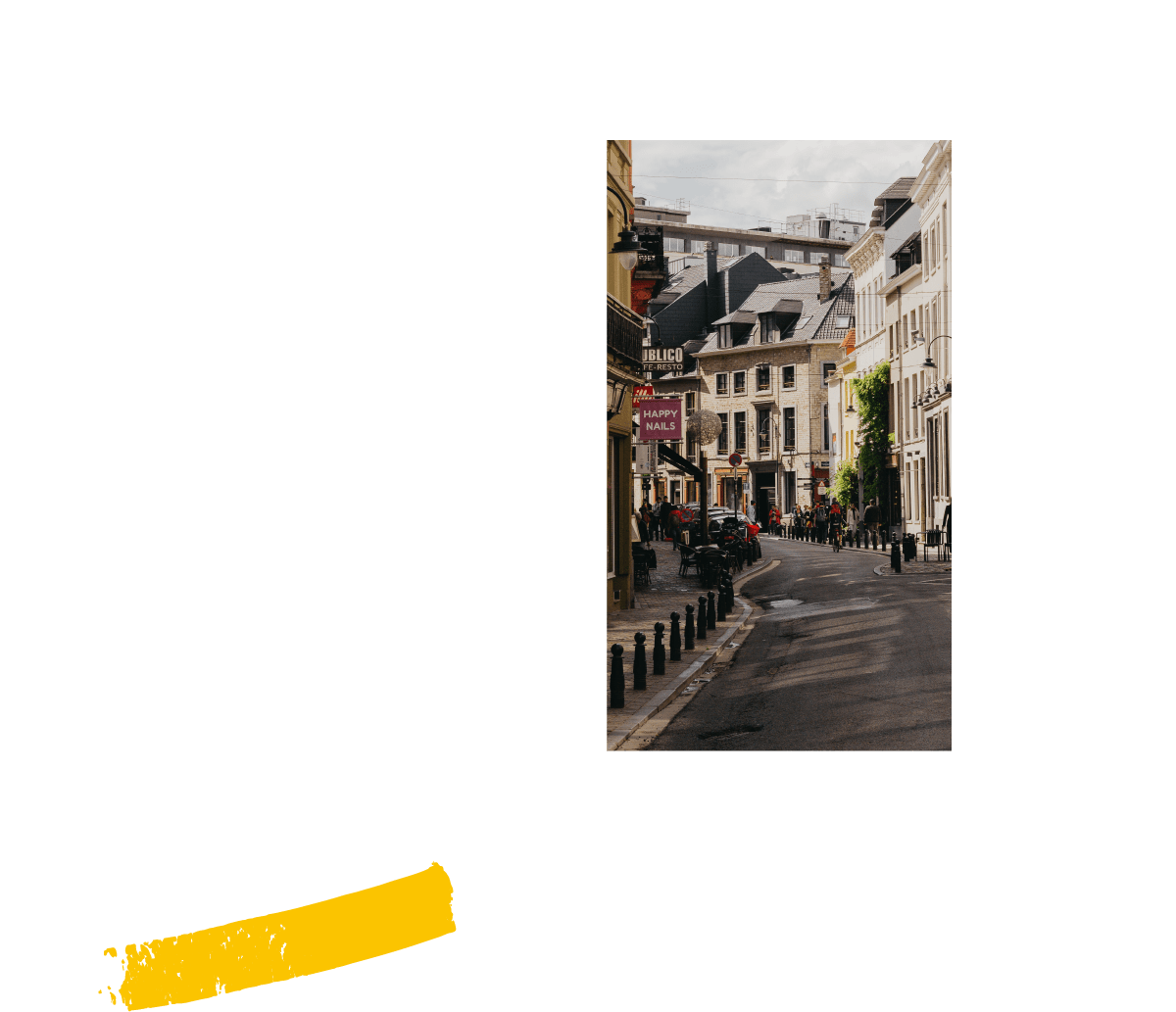
Who does Atlas® International move?
Literally, everybody.
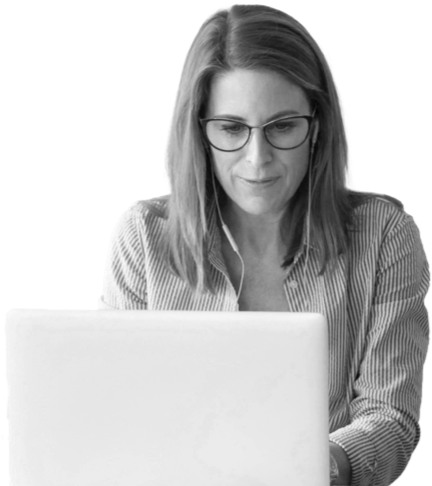
We're fluent
in the language of moving internationally.
Moving you from your current home to your next casa, maison, or 家 is kind of our thing. We’ve even got the numbers to back it up.
60+ Years of Moving Experience
400+ Movers in North America
17 Countries with Atlas® Movers
8 Industry Certifications
1 Mission to Help You go new places ®
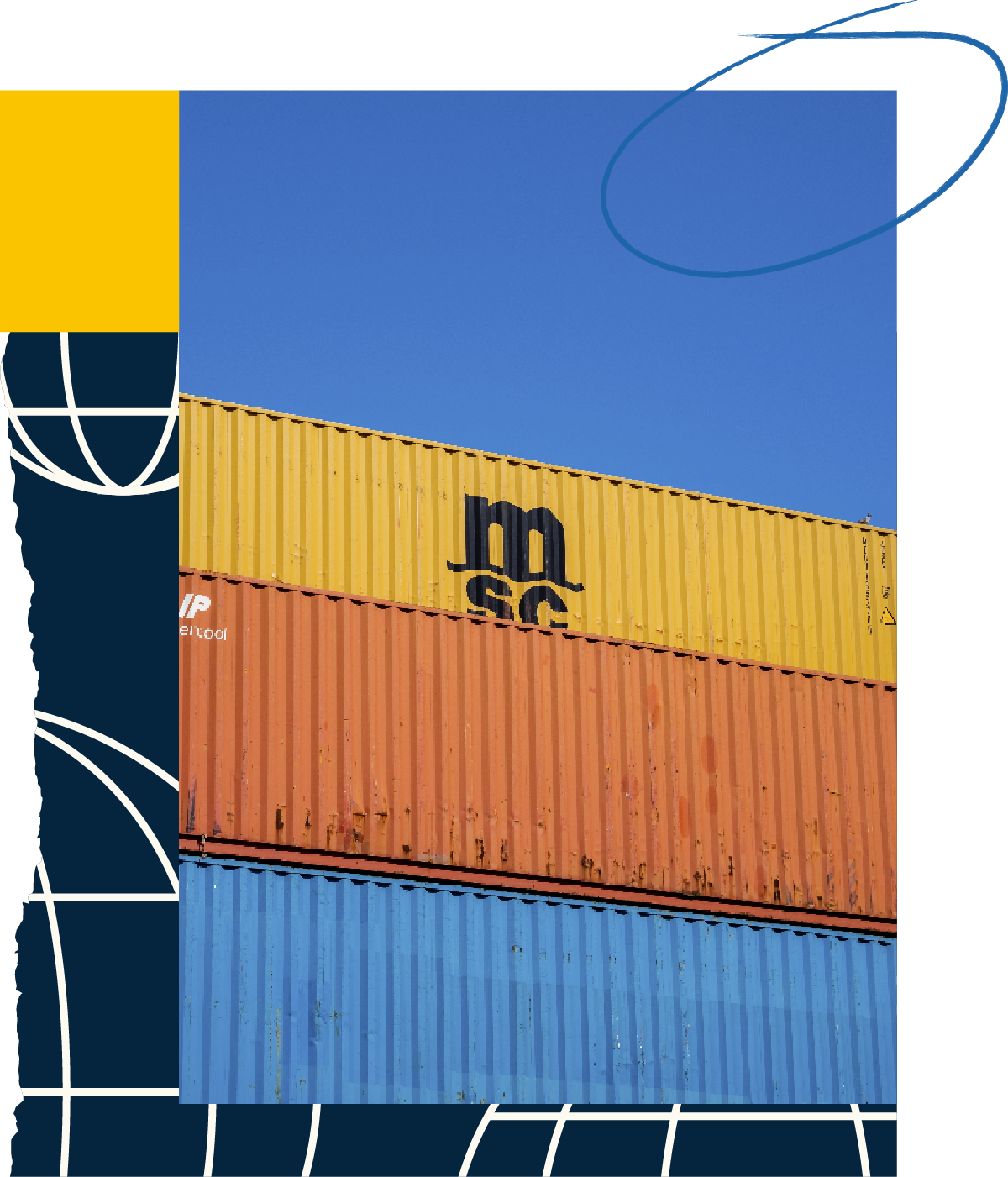
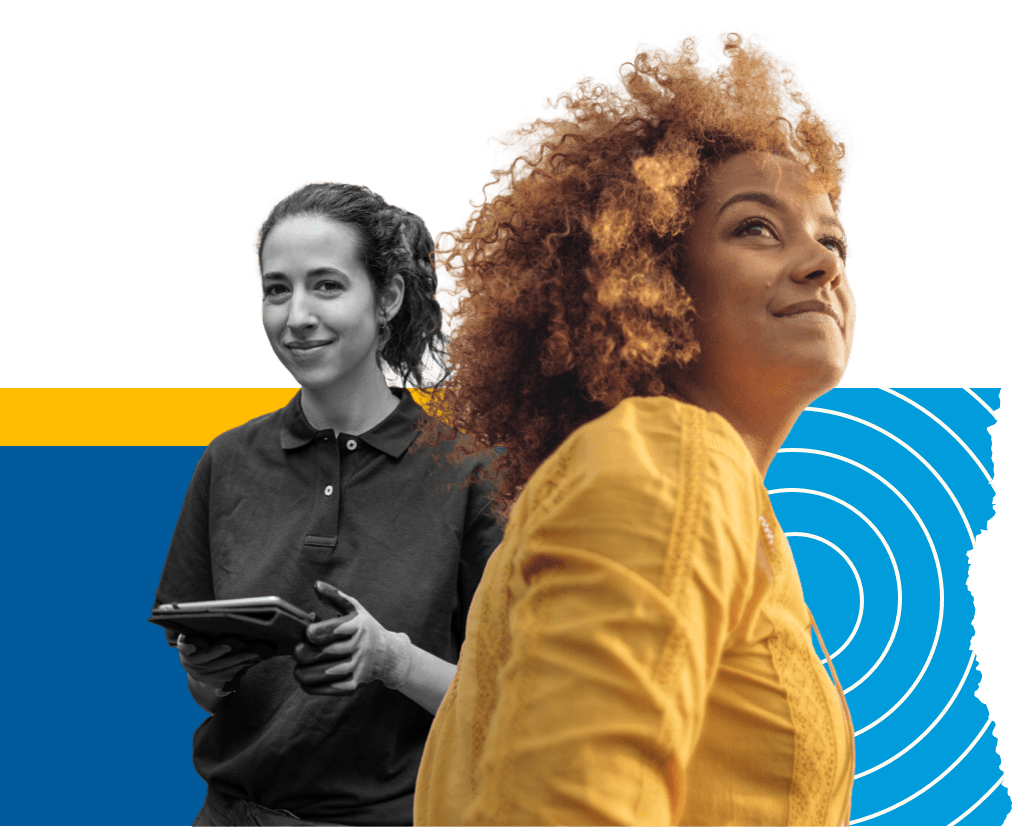
Working together is what moves us.
The international moving process is exciting! And we’re with you every step of the way.
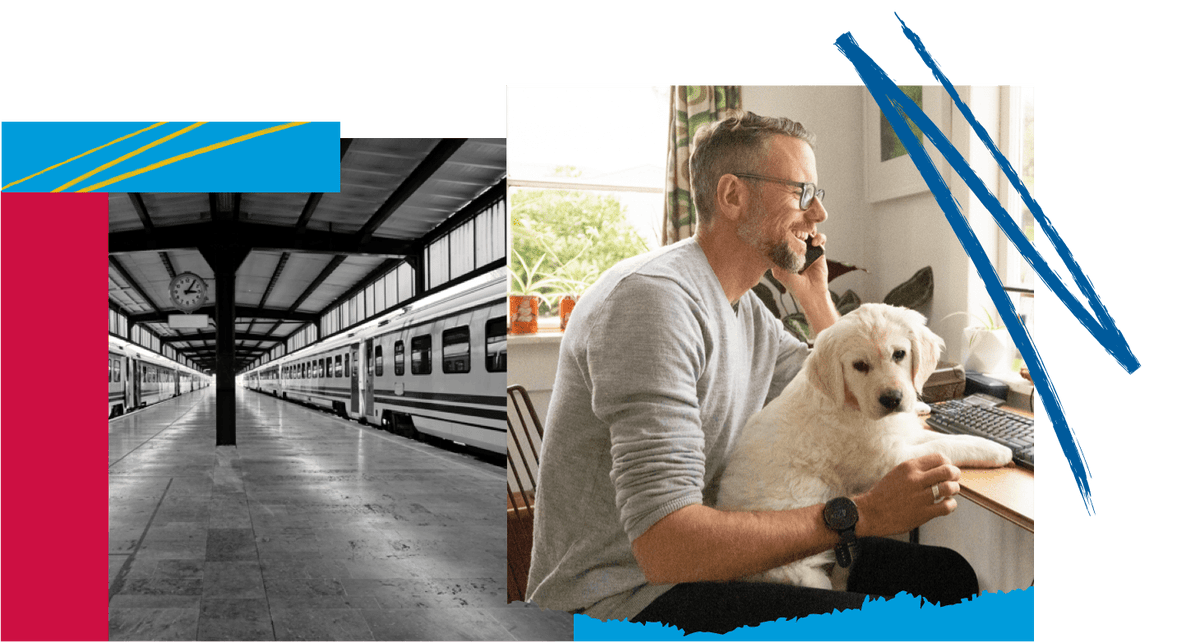
Kick off your international move by contacting us to get started on your free moving estimate. Together, we’ll nail down a plan of action.
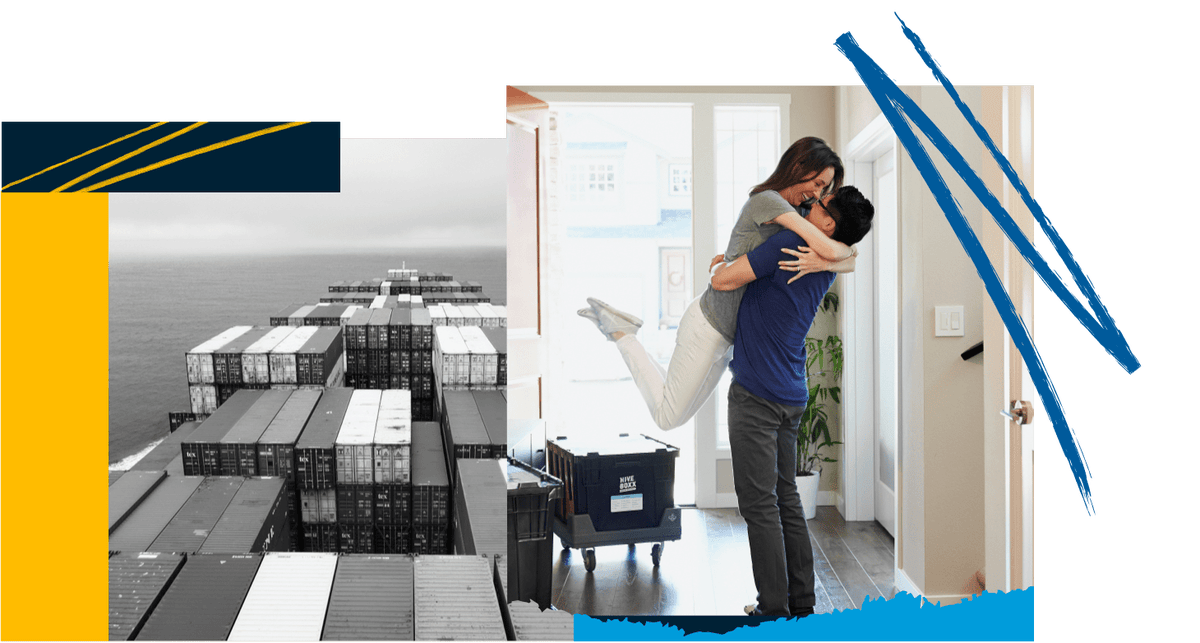
When it’s time to move your life overseas, our skilled moving crews will prepare your belongings for their journey by ocean or air to their new home.
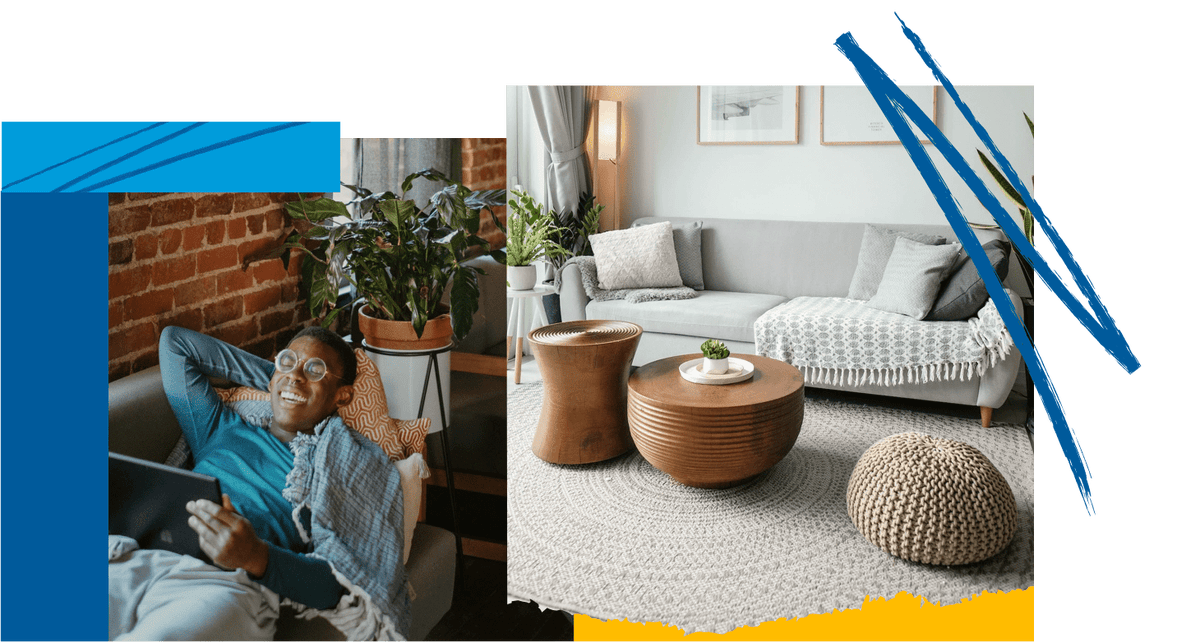
Once your belongings arrive at their destination and are cleared by customs, we’ll deliver them and help you settle into your new home sweet home.